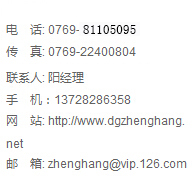
本周,正航儀器設(shè)備實(shí)驗(yàn)室主要介紹了鋼表面電弧噴涂鋁層的感應(yīng)重熔、重熔后噴涂層的微弧氧化以及微弧氧化陶瓷層的特性三個方面的實(shí)驗(yàn)結(jié)果。研究了重熔工藝參數(shù)對重熔效果的影響,對重熔后的噴涂層進(jìn)行了相分析,并對比了重熔前后涂層與基體結(jié)合性能的變化情況;找到了適于進(jìn)行微弧氧化的電弧噴涂鋁層的條件;研究了微弧氧化工藝參數(shù)對微弧氧化陶瓷層生長規(guī)律的影響;對微弧氧化陶瓷層進(jìn)行了X-Ray、SEM和EDS分析,測定了陶瓷層的耐蝕性能、耐磨性能以及復(fù)合膜層的抗熱沖擊性能。
如下,總結(jié)相關(guān)的實(shí)驗(yàn)結(jié)果:
(1)感應(yīng)電流、處理時(shí)間對感應(yīng)重熔效果有很大的影響,本文中當(dāng)感應(yīng)電流為300 A,處理時(shí)間為35 s時(shí),獲得的重熔效果最好;
(2)感應(yīng)重熔處理后涂層與基體之間形成了冶金結(jié)合層,重熔后涂層由表及里的相組成依次是:Al→FeAl3→Fe2Al5,冶金結(jié)合層的存在提高了電弧噴涂鋁層和鋼基體的結(jié)合強(qiáng)度,并因?yàn)殡姶艛嚢璧淖饔锰岣吡送繉拥囊苯鹳|(zhì)量;
(3)通過感應(yīng)重熔獲得無通孔的致密鋁涂層是在鋼表面制備優(yōu)質(zhì)微弧氧化復(fù)合陶瓷層的首要條件;
(4)微弧氧化陶瓷層的總厚度和向外生長厚度均隨電流密度和處理時(shí)間的增加先達(dá)到一極大值,然后在不同程度上都有所減;微弧氧化陶瓷層向內(nèi)生長厚度隨電流密度和處理時(shí)間的增加而增加;當(dāng)電流密度為15A/dm2、處理時(shí)間為28 min時(shí),陶瓷層厚度最大,約為87.3μm;
(5)通過復(fù)合陶瓷化技術(shù)獲得的復(fù)合膜層由表及里的組成分別為:陶瓷層→重熔電弧噴涂鋁層→鐵鋁化合物層,各界面均為冶金結(jié)合,并形成材料成分的梯度過渡;微弧氧化陶瓷層主要由α-Al2O3、γ-Al2O3、θ-Al2O3以及一些非晶相組成;
(6)微弧氧化陶瓷層由外部疏松層和內(nèi)部的致密層組成;膜層表面的放電通道在處理過程中數(shù)目逐漸減少,孔徑逐漸增大,陶瓷層表面有明顯的熔融固化跡象;
(7)從3%到20%的各種濃度的NaCl溶液中,經(jīng)過陶瓷化處理的試樣的耐蝕性能優(yōu)于重熔前后的沒有經(jīng)過陶瓷化處理的試樣;當(dāng)摩擦延長米大于60 m時(shí),微弧氧化陶瓷層的磨損失重小于45鋼的1/2;復(fù)合膜層具有良好的抗熱沖擊性能。(正航儀器試驗(yàn)室整理)http://www.hphzs.com